摘 要:文章结合陕煤化二甲醚项目备煤筒仓工程的施工实例, 主要从工程概况,支承杆、液压设备等材料及机具的选用,滑模系统的组装,混凝土浇筑工艺,钢筋绑扎,滑升施工等方面介绍了滑模施工工艺的组成及应用,纠扭、纠偏及其它技术方法;通过与其他较常规施工工艺相对比,分析了滑模施工的特点和优势,提出了与其相关的重要技术要素和安全措施,对类似工程的施工具有一定的参考价值。
关键词:备煤筒仓;滑模施工;平台体系;分析比较;技术经济
1·工程概况
陕西煤化100万吨二甲醚一期项目备煤筒仓工程为钢筋混凝土结构,由四个筒仓组成,单个筒仓储煤量为八千吨。筒仓基础为大体积混凝土筏板基础,直径21m,厚1.8m(从-3.1m~-1.2m)。从标高-1.2m~39.6m为外筒壁,壁厚350mm,直径20m。每个筒内侧有壁厚为200mm,高13m的混凝土内筒及煤斗梁柱支撑筒仓底部呈两个煤斗状。筒仓顶为倒锥平台形,筒顶平台以上为通长连体框架结构,局部为3层框架顶标高为58m。
2·滑升前期准备及滑模装置组装
2.1滑升前期准备
1)按施工方案准备材料及机具。①模板:根据仓内、外周长确定使用高度为1.2m,宽度为10cm~25cm的普通定型钢模板。②围檩:传递混凝土侧压力和振动泵的冲击力等侧向荷载,确保模板结构的圆形平面形状,内外分别用三道10#槽钢焊接固定,将模板与提升架连成整体。③提升架:提升架规格为1400mm×2400mm。用普通钢管、10#槽钢制作。④操作平台:均采用刚性滑模操作平台。用钢管、扣件、木方、木板等搭设。⑤支撑体系:用普通钢管搭设。
2)液压系统设计及设备选用。①千斤顶:使用GYD60 滚珠型,每榀提升架设置一只,随升井架、钢梁处布置两只,一次行程为25 mm,额定顶推力60kN,施工设计取其50%,即30KN。②支承杆:选用φ48×3.5mm 普通钢管,焊接接头错开率为25%,手提磨光机打磨。③液压动力:使用YHJ-56 型控制台,油压机试验压力为12Mpa,施工中油压控制在8Mpa,使用φ16、φ8 钢丝编织高压软管与各种分油器组成并联平行分支式液压油路系统,布管时尽可能使油路长短相近。
3)液压千斤顶行程试验及调整。为保证滑模的同步性,调整各千斤顶行程,使其在相同荷载作用下行程差≤5mm。通过对所有千斤顶测试及调整,使每个千斤顶的行程符合规范要求。
2.2滑模装置组装
该系统由模板、内外围檩、各向支撑、提升架及附属构配件组成。组装顺序为:基础面放线→竖立提升架→绑扎1.2m 高环筋→调节钢管→内外围檩→内外模板→安装滑模环形平台(先内后外,先上后下)→平台外挑随升井架→平台格栅及面板→液压系统→调试→插入支承杆→全面检查→试滑升→正式滑升→吊脚手及安全网→继续滑升。
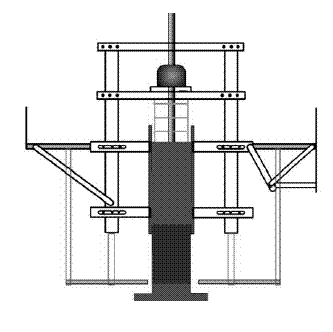
1 ) 提升架立柱尺寸为2400×200mm,用φ48×3.5mm普通钢管,按规格焊接成格构式构件,下横梁为双拼10#槽钢,上横梁为普通钢管,立柱与横梁螺栓连接。提升架就位时,应径向对准中心,下横梁上表面应在同一水平面上(保证千斤顶起点同步),提升架之间以短钢管互联成一体。
2)绑扎模板范围内的竖向、水平钢筋,接头按图纸要求错开。组装内外模板时,不仅要考虑几何尺寸,还要确保模板锥度。其中,内模锥度为2%~5%,外模考虑到变形因素,保持竖直即可。模板使用回形卡互拼(每条拼缝不少于3 个)。在模板上端第二孔、下端第一孔分别设双钢管围檩,以管卡勾头拉结模板(每条拼缝不少于2 个),围檩调节钢管与提升架立柱的连接。
3)刚性滑模平台用钢管扣件搭设双向,间距1000mm 的满桁架,支承在平台围檩上,平台围檩支承于提升架上,形成空间网架自平衡承力系统,桁架上按照设计规格绑扎木方,铺设木板或多层胶合板(木板接缝2~3mm)形成操作平台。这种操作平台刚度大,施工效率高,取材方便,容易加工制作。
4)液压提升系统是承担全部滑模装置自重、施工荷载和模板与混凝土间摩擦力并使其向上提升的动力装置,由支承杆,千斤顶、液压控制柜和油路等组成。
5)内外吊脚手架待滑升到一定高度时组装。在调节钢管及提升架立柱上,下挂吊脚手架,上铺脚手板,用于检查砼的出模强度,处理滑升过程中的质量缺陷,滑模后仓壁修整,清理出预留、预埋件,原浆抹光,库壁内粉等。挂脚手用钢管扣件搭设,高度从模板下口往下1.8m,挂脚手外侧用钢管连成围圈,增加其稳定性,并在侧面及底部满挂安全网、外侧三道钢筋围护以保证安全。
3· 施工工艺流程
3.1混凝土施工
20m以下采取汽车泵直接浇筑入模,20m以上采取汽车泵与拖式泵穿插使用配合入模。振捣手随着入模跟进振捣。砼浇灌时遵循连续交圈、变换方向的原则,以减小库壁扭转、倾斜的可能性。
3.2钢筋工程施工
钢筋采用绑扎搭接,竖向钢筋搭接长度大于40d,环向水平钢筋搭接长度大于50d,钢筋按25%接头率错头,仓壁钢筋边滑边绑,与砼浇筑交错穿插进行,钢筋保护层和位置通过设置在提升架下横梁上的钢筋限位卡来保证。
3.3 滑升工程施工
1)初升:模板的初次滑升,应在浇筑高度达900mm 左右及开始浇筑4h~6 h后进行。开始滑升前,必须先进行试滑升,试滑升时,应将全部千斤顶同时升起3cm~5cm,观察砼的出模强度,出模砼指按有微痕为宜,符合要求即可将模板滑升到30cm高。对所有提升设备和模板系统进行全面检查、修整后,可转入正常滑升。
2)正常滑升:当初滑以后,即可按计划正常分层浇筑砼,分层滑升。正常滑升时,两次滑升之间的时间间隔,一般控制在1.5h 左右,每个浇筑层的控制浇筑高度为30cm。
3)末升:当模板滑升到距顶1m 左右时,即应放慢滑升速度,并进行准确的抄平和找正工作。整个模板的抄平、找正,应在滑升到距顶标高最后一层以前做好,以便顶部砼均匀地交圈,保证顶部标高的精确度。
砼全部浇筑结束后,应及时卸去平台上所能卸去的荷载,并按正常滑升时间继续提升模板。支撑杆之间以弧形钢管连结加固。模板下口滑出库壁时停止滑升。最终按照油管→千斤顶→液压控制台→外吊架→内平台→桁架梁→“开”字架→内、外模板的顺序拆除滑模装置。
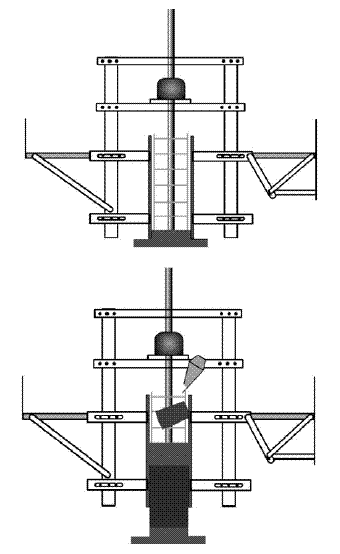
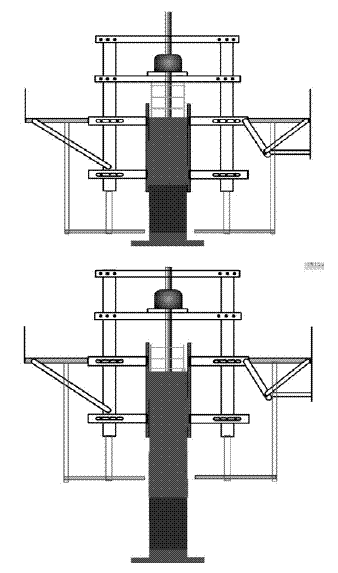
4·滑模提升和移动过程中的一些技术要点
4.1滑模初次滑动时,运动的间距切忌太大,否则容易造成脱模等安全事故的发生;
4.2是先进行缓慢的移动,用来确定出滑模运动的时间和速度的要求,是实现快速作业的前提条件;
4.3准确把握滑行时间和速度以后,将每层混凝土的浇筑高度为20cm~30cm 之间,确保混凝土振捣和浇筑的质量;
4.4在滑模连续操作过程中,必须对钢筋的制作安装进行合理的安排。因为滑模的施工过程具有连续性,其钢筋的安装量非常大,不能因为钢筋安装不及时而影响滑模施工的进度;
4.5在滑模的施工过程中,因为滑模具有移动行,容易出现位置的偏差,应及时进行纠正,严防施工安全事故的发生。
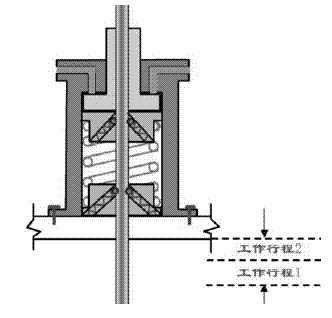
5· 质量控制及滑模纠偏纠扭措施
5.1纠偏纠扭前期准备
组装时,在库外侧轴线上对称方向一圈挂设四个15kg 大线坠,滑升60cm 后在承台面相应位置做出对中标志,滑升时,每90cm 检验一次对中标志偏移值,纠偏纠扭时每30cm 检验一次,由专人负责做好记录。
5.2纠偏纠扭预防控制方法
1)在支承杆上每30cm 划线、抄平,用限位器按支承杆上的水平线控制整个平台水平上升,进而保证结构竖直。
2)砼浇筑遵循“分层交圈、变换方向”的原则。分层交圈即按每30cm 分层闭合浇筑,以防止出模砼强度、摩阻力差异大,导致平台不能水平上升。另外,平台上堆载应均匀、分散。
3 )纠偏采用倾斜平台法,当发现垂直度偏差超过10mm时,将平台反向倾斜5~10cm,通过倾斜提升达到纠偏的目的。
4)当发现平台扭转时,按扭转反方向,沿库壁6 个位置用钢筋斜向焊于库壁竖筋于提升架下横梁上,通过滑升时钢筋收紧产生的反向扭力进行纠扭。
5)纠偏纠扭应遵循勤纠正,小幅度纠正的原则;观测得到的偏移值须结合沉降观测数据加以分析。
6·滑模工艺与其他施工工艺简单技术经济对比分析
上面主要介绍了滑模施工的具体施工工艺及技术质量控制措施。针对备煤筒仓结构工程下面具体选三种施工方案从施工工期,质量安全及经济效益等方面分别进行分析比较。
6.1工艺简单介绍:
工艺一:滑模施工(上面已详细说明)。
工艺二:常规混凝土结构施工:内外侧搭设双排脚手架,翻模施工,类似于以往烟囱组装层以下施工或灰库施工。
工艺三:三脚架体系施工:
采用翻模体系,内外操作架为施工平台。
6.2三种工艺施工工期分析比较
工艺一:滑模施工正常情况下每天平均施工约为2.5m~3m,且两个筒仓一起用一整套液压泵控制同时滑升,滑升时间约为15d,加上系统组装及系统拆除各按一周考虑,合计施工周期约为30d。
工艺二: 用常规翻模施工工艺,根据以往类似工程施工经验,直径20m,高度约40m,壁厚350mm的两个筒仓筒壁施工按照三天一节(钢模板用烟囱施工用标准模板一节按1.5m计算),平均每天0.5m,正常情况下施工周期约为80d。
工艺三: 三脚架施工就按照以往冷却塔施工速度,两个筒仓同时施工平均每天一节(模板用以往冷却塔施工用模板一节按1.3m计算),平均每天1.3m,正常情况下施工时间约为31d,加上系统组装及系统拆除各按一周考虑,合计施工周期约为45d。
6.3三种工艺施工质量分析比较
从施工质量角度分析比较,首先,无论是工艺二(常规翻模施工)及工艺三(三脚架体系),均为翻模施工,环向施工缝及竖向拼缝较明显。第二,工艺二及工艺三均需要三层模板进行翻模,全部靠人工操作,混凝土外观存在水平缝及竖向拼缝质量问题。但是如果采用工艺一滑模施工,模板只需要支设一次,且平台体系理论上是刚性体系,不仅对圆形结构的圆弧度控制能得到有效保证,不用反复调整半径,而且混凝土的连续性比一般的施工方法要好得多,机械化程度高,虽然刚出模后混凝土外观质量略差,但及时修补收面后表面效果较好,连续成型没有环向施工缝,也没有环向及竖向模板间拼缝的痕迹。混凝土的密实度、光洁度较好。
6.4三种工艺施工安全分析比较
从安全角度分析比较, 首先,工艺一滑模体系与工艺三三脚架体系略同,平台板及维护栏杆均需要很频繁的拆除、移动、翻倒,造成不安全隐患大大增加。第二,从上面比较分析的施工工期上可以看出,工艺二常规翻模施工施工周期最长,工艺一滑模体系施工周期最短,施工工期短,安全风险相对比例也较小。
6.5三种工艺施工投资费用分析比较
首先, 从劳动力用工情况进行分析比较,综合三种工艺各自所需要施工的总周期与平均用工,算出总工日数来进行比较。以同时施工两个筒仓筒壁为例,滑模工艺根据实践得出在正常施工情况下50人施工30天,总工日数约为1500个工日,平均按100元/天计算,需人工费约15万元;常规翻模施工按照以往经验正常情况下60人施工80天,总工日数约为4800个工日,需人工费约48万元;三脚架工艺施工按照以往经验正常情况下60人施工45天,总工日数约为2700个工日,需人工费约27万元;
其次, 从模板及架子的投入费用上,滑模工艺只需一层模板,节约了常规翻模施工模板投入的三分之二。不需要脚手架搭设,节约了常规翻模施工大量脚手架长时间占用的租赁费用。且能极大地减少模板的周转次数和支护时间,大大降低了模板的损耗;
第三,滑模装置、滑模设备及支承杆是滑模施工中的一套临时性设施,不是结构本身的组成部分,其一次性投资费用相对较大,但理论分析与实践证明,滑模施工在一个工程中摊销的成本并不比其它工艺施工的费用大,相反,只要具备一定的通用性,维护良好,其综合效益明显,尤其是在市场化后的现在,滑模工艺更体现了它的综合优越性。
7· 滑模施工工艺施工效果与结论
施工记录表明:筒体半径、壁厚、截面尺寸、表面平整度等各项误差指标均满足《液压滑动模板施工安全技术规程》和其它强制性文件相应条款的要求,而且完全消除了施工缝大大提高了结构的整体性和安全性;避免了大量人员作业时的种种不便及安全隐患,缩短了施工工期,缩短了设备及器具的租赁时间,减少了劳动力用工,从而很大程度上节约了施工成本。另外,滑模施工连续推进,充分保证了结构外观的圆顺。总之,滑模施工有良好的应用价值,在类似结构中尤其是在如筒仓结构的等截面建筑物结构施工中能得到广泛应用。