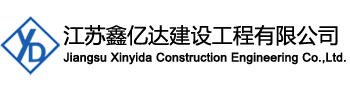
提高混凝土拌和站生产合格率探讨 |
日期:2016-3-17 14:13:30 来源:互联网 浏览数: |
根据规范要求,混凝土拌和站各种物料配料精度应满足:骨料±2%,水泥、水、外加剂、掺合料±1%;连续生产作业时,配料精度总合格率不低于90%,超差的10%仅允许掺合料、外加剂的允差,其数值为±3%。减小配料误差是提高混凝土合格率的保证,但是由于多种原因限制,目前国内大多数拌和站的配料精度都难以达到规范要求,单盘配料误差甚至达到允许误差的几倍,总体生产超标率有的甚至达到20%以上。
2·配料误差的成因分析 2.1 拌和站配料过程描述 2.1.1 操作员收到试验室提供的施工配合比后,在拌和机上输入生产配方,物料设定的配方重量设定为W0。 2.1.2 在生产控制界面启动自动生产,拌和机设备会根据配方上各种材料重量,开始上料。 2.1.3 物料流动的下达到秤中,秤会将重量通过称重传感器转化为弱电信号(毫伏级别),并将信号传送给仪表,仪表将该弱电信号经放大、滤波、AD转换及数字处理变为数字显示的重量值W1。这个信号传送及处理的延迟时间范围我们设定为t1。 2.1.4 当称重值W1接近配方值时,控制系统下达关断配料信号,该信号经控制继电器关断交流接触器或电磁阀电源,从而关闭配料门,该过程处理时间我们设定为t2;在t2时间范围内,物料继续流入秤中。 2.1.5 配料阀门关闭后,已经流出阀门的,还未落入秤中的物料继续下落,逐渐落入秤中,直至落入完毕。这段时间我们设定为t3,t3的时间长短由配料阀门出口和秤中物料垂直距离决定(即落差)。 2.1.6 这时,秤上的重量为W,W为最终配料重量。误差E=W-W0。 2.2 配料误差来源的理论分析 配料过程中,最终配料重量W与下达关闭配料阀门时的重量W1的差值,我们称之为过冲量ΔW,ΔW=W-W1。只要过冲量ΔW是确定的,控制系统要准确实现配方W0的配料量,只需在秤值达到W1=W0-ΔW时关断供料系统即可。但ΔW受到种种因素的影响,它的准确值是未知的,控制实践中通常用一个预估的过冲量ΔWa进行配料控制。 替代值ΔWa与ΔW实际值的偏差造成本次配料的误差(绝对误差)。所以生产误差是一定会产生的。 2.3 配料误差来源现实分析 上文中提到,配料控制误差来源于过冲量替代值ΔWa与实际值ΔW的偏差E,E=W-W0=ΔW-ΔWa,根源在于组成ΔW的各要素的不确定性。 2.3.1 不确定性要素一:供料器出口瞬时流量。过冲量的大小与供料器出口瞬时流量成正比关系,该瞬时流量受到骨料和粉料仓物料起拱、细骨料粘结、以及传送装置故障的影响,并不是匀速的。 2.3.2 不确定性要素二:阀门关闭的响应时间。当系统下达出料阀门关闭命令后,阀门执行机构开始执行。一些气动执行机构由于受气源气压、机械润滑、块料挤压等因素影响,响应较慢,导致阀门关闭延迟时间不定。 2 . 3 . 3 不确定性要素三: 物料下落时间( 落差)。对于同一台搅拌设备,配料重量越大,落差越小。由于不同标号混凝土配方多变,落差变化频繁。 2.3.4 其他影响配料误差的因素:机械设备原因。除以上不确定性因素外,机械设备本身的故障是配料产生误差的又一大原因,如:配料阀门关不严,导致漏料;秤没有及时校正,因各种干扰原因称量抖动;电压不稳,导致设备运转不平稳等等。 3·基于现有拌和设备配料误差的控制 从配料误差成因分析中我们看出,要减少现有拌和设备的配料误差,首先要从设备本身存在的问题着手: 3.1 减少供料器出口瞬时流量波动 对于流体物料(水和液剂),调整各阀门的合理开度,控制液剂流量平稳。根据配料重量,合理调整快配值。 对于粉料,流量波动主要致因是粉料仓物料起拱;应保持合理的粉料储量和储存时间并合适调整粉料仓的破拱压力,保持压缩空气干净,实现粉料的顺畅下料。 对于骨料,流量波动主要致因是细骨料粘结及缺料;应保持骨料仓的物料有一定储量,实现稳定的物料流供应;选择使用合格稳定的原材料供应,防止过大骨料或泥块等堵塞出料口并采用合适的破拱手段(如振动)保证落料流畅以减小流量波动范围。 3.2 减少阀门关闭的响应时间 提高机械执行机构响应的可靠性是减少阀门关闭响应时间的根本途径,平时要保持良好的机械润滑和动力气源气压稳定等。 3.3 减少落差波动对误差的影响 由于配料重量越大,落差波动对误差的影响越小,所以尽可能采用HZS120以上的拌和机并且尽可能每盘打料1.5方以上。 3.4 定期设备保养 设备的定期维护保养、仪表的定期校准,有助于及时发现设备故障,减少错误发生的概率。 3.5 改造生产控制系统 为了减少误差,除采用第三章中的四种常规办法外,还可以对生产控制系统进行改造,可通过以下功能减少生产误差: 3.5.1 适合的过冲量设置。上文中提到,只要过冲量设置合理,即可减少配料误差,在系统使用过程中,找出适合本拌和站生产多种型号混凝土对应的过冲量;对操作手进行再培训,保障在后续生产过程中能够根据生产混凝土的变化及时找出符合该混凝土的过冲量。 3.5.2 自动点动配料功能。点动配料是指在配料达到设定值前,暂停配料,尔后以给定的时间(该时间内进料量小于最大允许误差)循环点动开启配料,直至配料合格。 3.5.3 超料超差的补救措施。点动配料不可能每次成功,当点动配料失败时,系统依旧提供补救措施:即超秤扣秤;该措施坚持在绝不欠料超差的原则下,对适扣秤提供精确点动扣秤操作以最大限度的改善配料合格率。 3.5.4 快、慢喂料结合的供料机制。以上三种办法都为工控系统本身的解决办法,为从根本上解决生产精度,还可以与机械设备改造相结合,对机械设备的供料方式进行改进,在原有供料机制基础上:改进为“快、慢喂料结合的供料机制”。该方法的原理是:初始供料时采用正常的快速供料,保障生产效率,在称重重量接近配方一定范围时,关闭原有的快速供料阀门,通过加装的慢喂料通道供料,即减少材料流速;由于慢喂料流速小,过冲量小,会显著地提高计量精度。快、慢喂料结合的供料机制,既能保障生产效率,又能提高计量精度,是降低最大配料误差的一种途径。 |
相关阅读 |
上一条:中小学校舍抗震加固方法探讨 下一条:混凝土裂缝处理措施 |